Next Generation of Biogas Production
NextGas PowerBox
The power of the PowerBox
The NextGas Powerbox is a biogas plant housed in a container, featuring 1 to 4 biogas reactors along with pumps that efficiently feed and discharge the liquid manure.
A biogas reactor produces around 80kWh of biogas or around 25kWh of electricity. Around 1.4 to 1.8 m3 of farmyard manure are required per day.
This makes it possible for smaller farms to produce biogas. Farms with 50 - 100 cows and 2 - 4 reactors are ideal, as they can efficiently produce electricity and heat for their own use or create an additional source of income by feeding it into the grid.
The NextGas PowerBox is fully automated and data-controlled. This enables low operating costs. Irregularities are recognized at an early stage and, in the best case, automatically rectified.

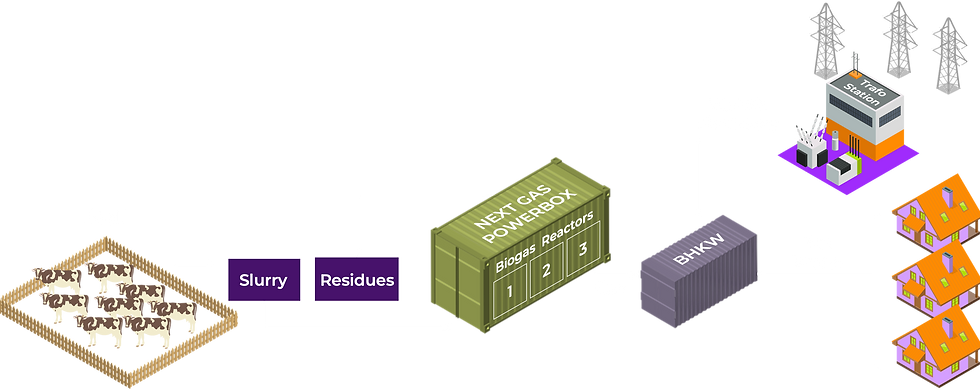
The PowerBox on your farm
The biogas system in the PowerBox container can be set up and connected to the power grid quickly and easily with little planning effort.
short planning time and installation
simple operation
predictable cost
stable return
high profitable
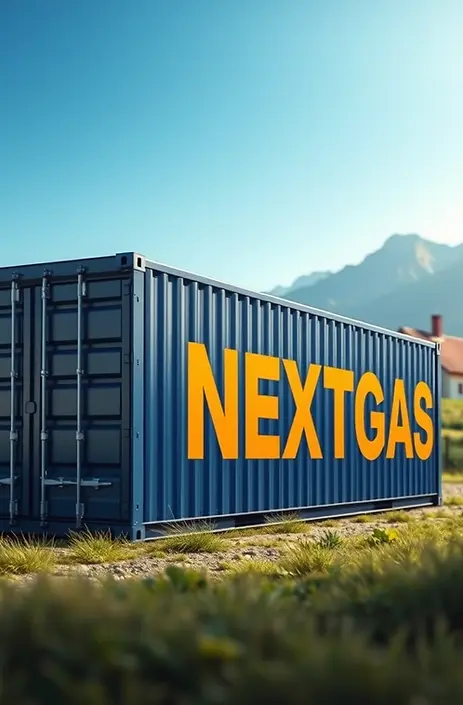
Planning Information
What does it take to build a biogas plant? Contact us for a first exchange. These are just some of the questions to discuss:
Infrastructure - Do you have two manure holes? Do you have a space large enough for a 12 meter container and a container with a gas engine? How far away is this space from the manure holes? How far is the site from the transformer station?
Size - How much liquid manure do you have per day in summer and winter? How much electricity does the farm consume? What is the heat requirement of the entire farm? How do you cover your electricity needs and how do you heat today?
Project Planning - Is the biogas plant located in the agricultural zone? Have you already spoken to Oekostromschweiz about CO2 reduction certificates? What options do you have to pre-finance the investment?
Standardized
The PowerBox is a fully standardized product which is pre-produced at the factory and shipped to you in a 12 meter container. It is modular to adjust the number of reactors to the size of your farm. This approach makes planning and installation short and predictable.

Data driven
The mechanical process is fully automated and controlled. The biological process is constantly monitored by several sensors. The measurements are continuously analyzed so that changes can be detected early. The learned data is modeled in a digital twin to simulate the best conditions for optimal gas yield.
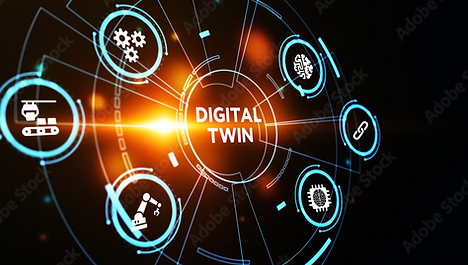
Managed fermentation
The automation and data analytics allows to maintain the optimal environment in the closed reactor vessels. The optimal environment for an effective methanogenesis is dependant on various parameters like pressure, temperature, pH-value and retention time. The ability to keep all parameters stable enables the solution to produce a consistently high gas yield.
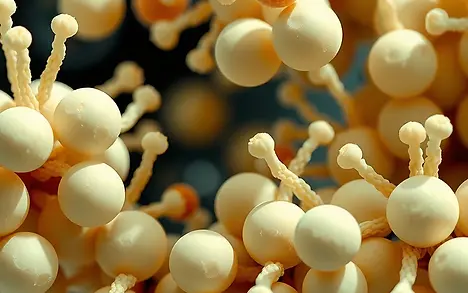
The process in the reactor is virtually modeled and optimized in a digital twin
